Describe the Production Process Steps Used by Toyota
The following are common types of production process. Identify an opportunity an objective for improvement explore new ideas by consulting with your employees break the objective down into sub-objectives or deliverables plan the tasks for each sub-objective without overlapping human and material resources or timeframes.
This second meaning is sometimes referred to as Ninbennoaru Jidoka which literally translates into automation with a human.
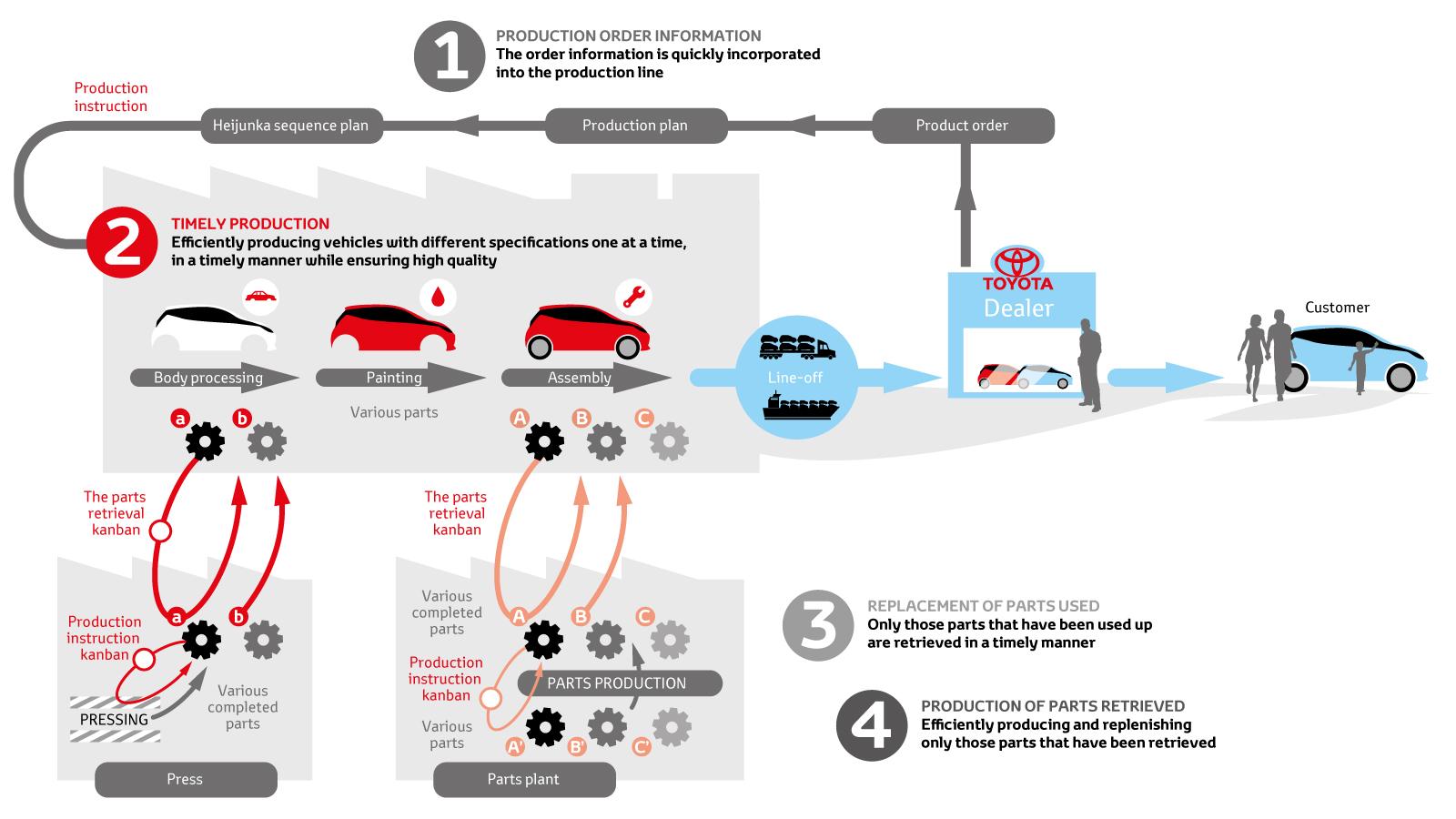
. Only producing what is needed and not storing excess inventory and Jidoka. The two main concepts that drive The Toyota Way are Just-in-Time. Integrating robots has also helped to decrease waste products saving company.
Job Production The process of creating a single item. The Toyota Production System historically has had four basic aims that are consistent with these. 132 is a graphic representation of equation 2 which is the short-run production function for radios.
Getting to immediate root cause when production runs into problems. Morgan and Jeffrey K. This involves following various steps which start at the input stage of product creation to the output stage as they sell to customers.
The system is credited to Taiichi Ohno 3 and actually most agile methodologies used especially for software production nowadays have been inspired by the TPS. A production process is a series of steps that creates a product or service. He says this is the meaning coined by Toyota.
The kanban system is central to the just-in-time process providing an automatic real-time method. From this book we learn that Toyota does more than Lean manufacturing they also have Lean Product Development System LPDS. How Toyota uses automation to improve processes.
The goal of the Toyota Production System is to provide products at world class quality levels to meet the expectations of customers and to be a model of corporate responsibility within industry and the surrounding community. But in order for it to expand into something tangible Toyota puts each vehicle proposal through a series of five important and very deliberate processes designed to transform it into a complete yet still original-looking product. For example a machine shop that produces an industrial part ordered by a customer.
As parts are used up new stock is delivered at the right time in the right quantity so there is no interruption or slow-down in the production process. In the Toyota Production Development System James M. Typically applies to unique items or things that have low demand.
Has two meanings the first is automation in the usual sense to change from a manual process to a machine process. The part sequencing and setting up schedule is. Definition and Types for Businesses To Use.
Toyota is using automation to help improve their production processes for many years. They have been providing greater speeds and increased efficiency in a variety of domains such as textile machinery and automobile. Rumour has it that Taiichi Ohno inventor of the Toyota Production System refused to read past the first page of any report.
Every customer-supplier connection must be direct and there must be an unambiguous yes-or-no way to send requests and receive responsesToyota has created outstanding relationships between each person and the individual who is responsible. The production function is a short-run production function because it illustrates what happens to output as more and more units of the variable input labour are added to the fixed stock of capital. Liker explain how Toyota can develop a new car in 15 months while their competition needs at least 24.
Developed between 1948 and 1975 by Japanese engineers the system is still evolving today. Toyota was taking three steps to fight supply chain risks that he expected would be completed in roughly five years. In response his team created A3 address and summarize problem-solving on one side of A3-sized paper.
To manage the quality in all organizational management system the Toyota Production System incorporates different modernisms like strategy or kanri Hoshin use overall. The Toyota Production System is seen as a set of best practices for manufacturing. The material to flow through production assembly line and to be managed through TPS Toyota production system by which each assembly line help create final product in form of vehicle.
The detailed step through every process keeps Toyota moving smoothly and efficiently. Through inventory and half the bottlenecks at half cost and time the adopters of TMS Toyota Management System are authorized to manufacture twice above the normal production. Thus the machines were automated to identify and stop immediately when a defect or deviation occurs in the products or parts of the product.
The 6 steps of the Kaizen approach. In Toyota they used this term to indicate that the systems need to be automated to highlight and attract attention to any deviationsdefects originating in the production process. The first is to further standardize parts across Japanese automakers so they could share common components.
The key operational activities for Toyota production include transforming input raw material into final product. In this book the authors describe 13 Lean. The second meaning is automatic control of defects.
When a company creates products and goods to sell to consumers they typically use a strict production process. The A3 technique played a huge part in Toyotas success and all kinds of industries have since adopted it. The term Lean came later in the.
The concept of lean manufacturing is a more generic way to refer to the techniques and approaches pioneered by Toyota.
The Toyota Production System Tps Kanban Zone
The Toyota Production System House 5s Today
The Core Principles Of The Toyota Production System 37 Download Scientific Diagram
No comments for "Describe the Production Process Steps Used by Toyota"
Post a Comment